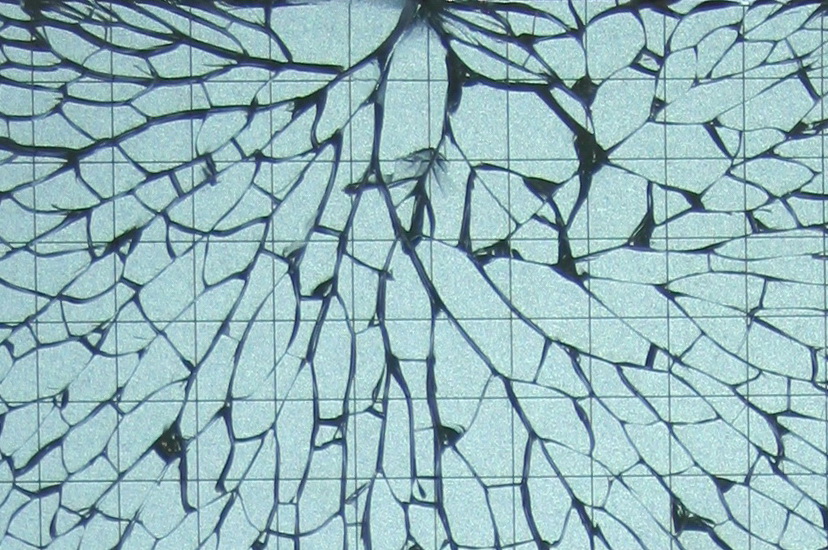
Silicate glasses are considered one of the "most brittle" materials in public opinion. However, at the micrometer scale the material shows sign of plastic deformation.
My work in this field concentrates on understating how microscopic plasticity can effect the macroscopic loadbearing capacity of sodium and soda-lime silicate glasses (commonly known as structural or window glass).
It is a well-known phenomenon, if a windshield of a car is being hit it develops a spider web-like crack pattern. The phenomenon responsible for the crack branching lies in the microstructure. When the rate of the released elastic energy reaches a critical value (which is needed to open a unit crack length) the forming crack finds a way to dissipate more energy. As a result, the initial crack splits up into two branches.
More about the high-speed experiments conducted on tempered glass specimens can be found in our previous paper.
In the framework of the MultiSil (ANR-13-BS09-0012) project in collaboration with Anne Tanguy (INSA de Lyon), Etienne Barthel (ESPCI), Guillaume Kermouche and Patrick Ganster (MINES) I studied the atomistic mechanism (details here and here) and the final load bearing capacity (more here) of different silicate glass compositions. The developed yield criterion was implemented in a finite element code (details here), which provided the opportunity to compare and fine-tune our model with real life experiments. Micropillar and microsphere compression tests allowed us to precisely identify the material constants and to propose a physically based yield model, for macroscopically brittle materials. An impressive video can be found here as supplementary material, which shows that silica glass (a macroscopically brittle material) can be deformed a room temperature like play dough.
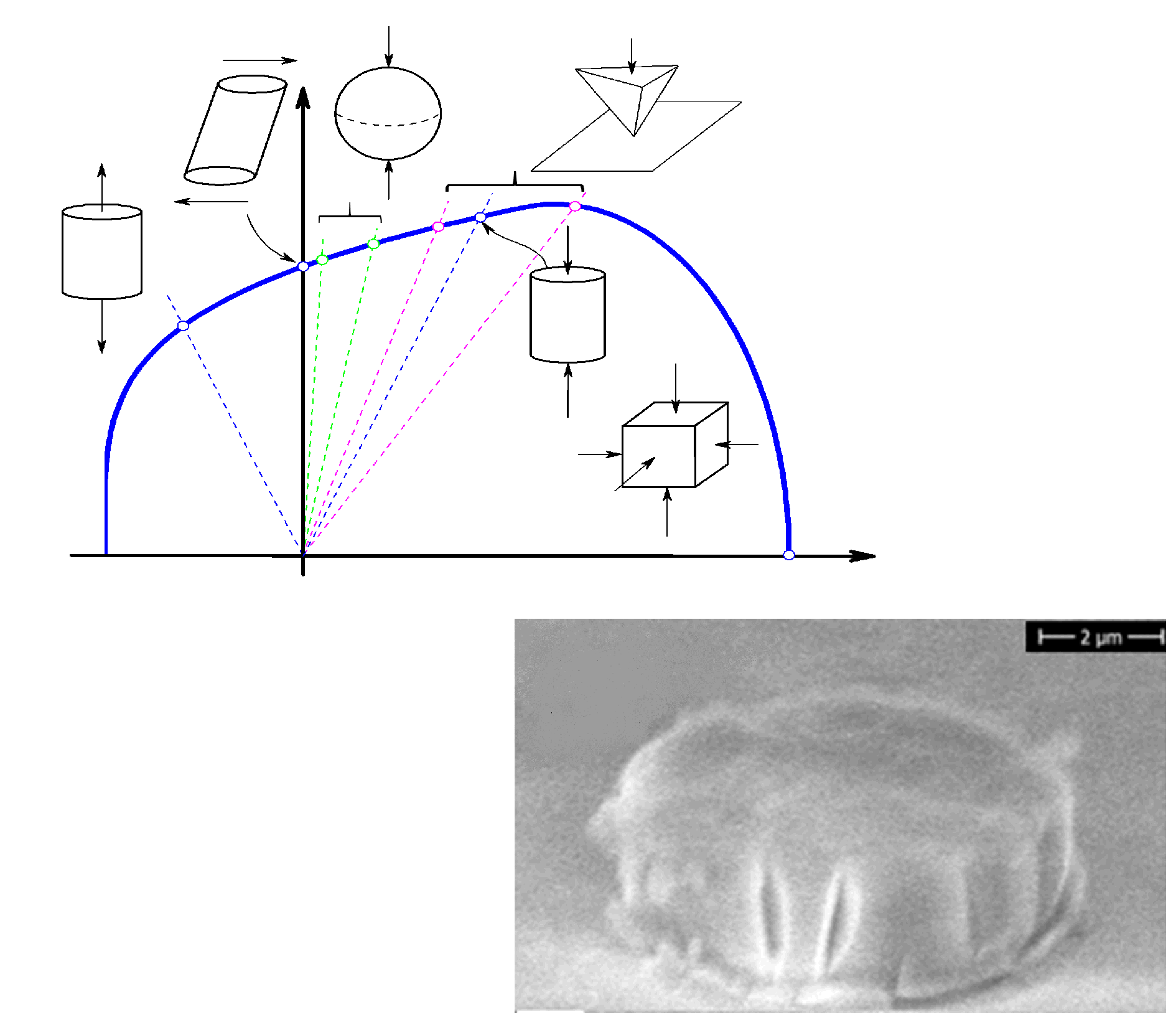
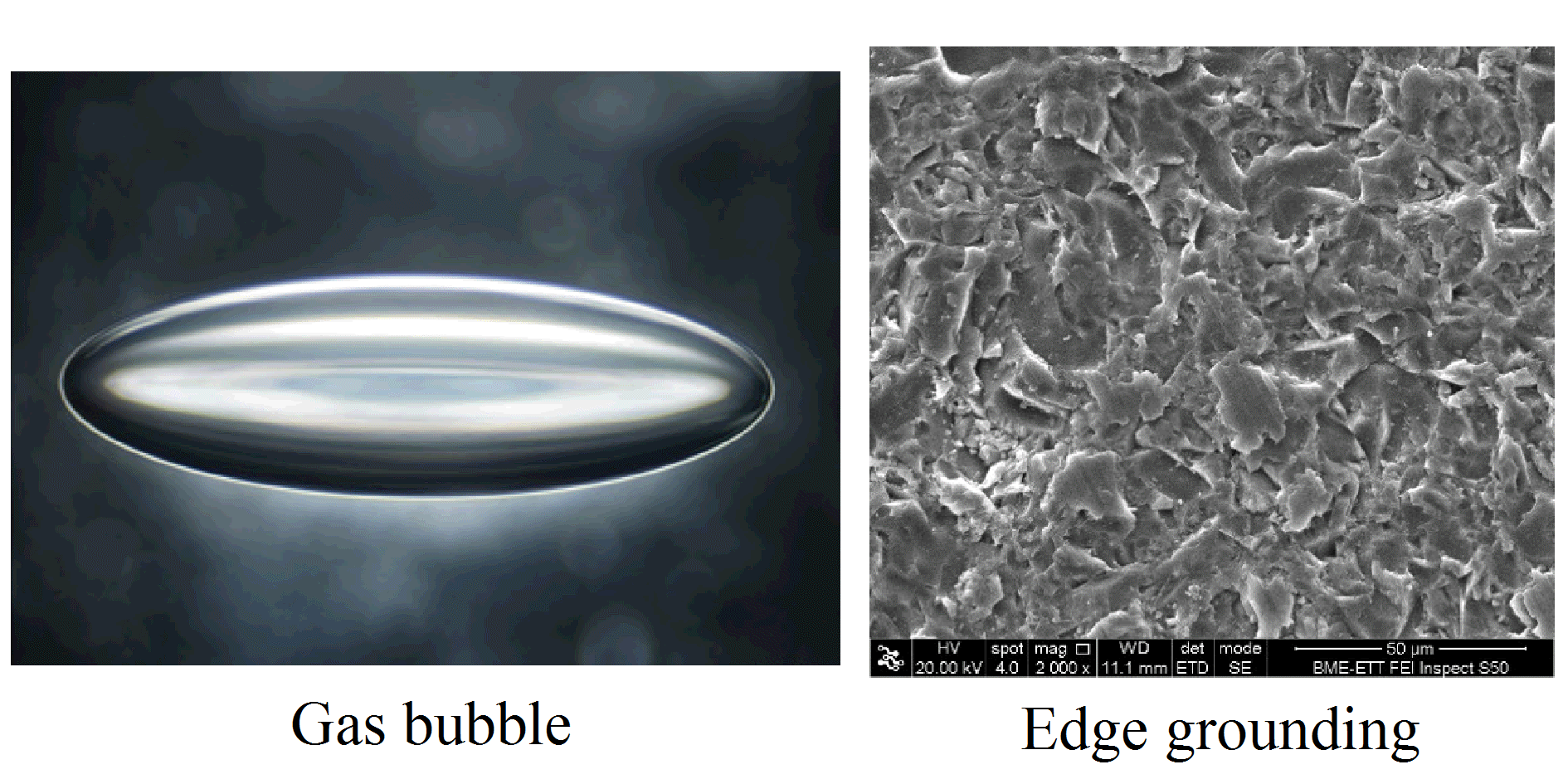
Compared to the high yield strength (~6.5 GPa) observed in micro-scale simulations and experiments, the macroscopic design value (0.08 GPa) is several magnitudes lower.
The reason explaining this phenomena lies in the meso-structure. Due to the manufacturing process, microscopic defects are introduced into the glass plate. Due to the covalent bunds between silicon and oxygen, which give the primary strength of the material, the plasticity remains at the crack tip. Therefore, the stress cannot redistribute, as it is shown in metals.
We have used atomic force microscopy and micro X-ray tomography to map and study the geometries of these defects. And indeed we have shown that these defects can cause significant stress increment, which results in the reduction of the macroscopically observed resistance. More about the defects and their stress fields can be found here and here.
The presentation I gave at ESPCI on the 17th of November, 2017 can be downloaded here: Presentation